Apr 15, 2024
Boeing to Urge New 787 Checks Linked to Jet’s Multiyear Review
Bloomberg News
,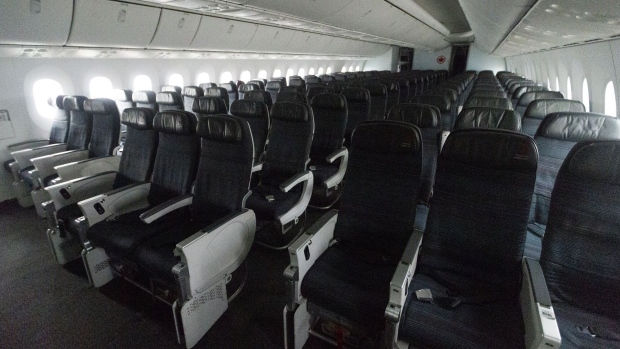
(Bloomberg) -- Boeing Co. is recommending that operators of its 787 Dreamliner inspect a nose component that helps maintain cabin pressure, a consequence of the plane’s tip-to-tail review in recent years that gained urgency amid fresh allegations it cut corners.
Boeing engineers said they’re discussing the visual inspection of the part with US regulators following a multiyear study of the structural integrity of the US planemaker’s marquee wide-body plane.
Speaking to reporters at the company’s 787 factory in North Charleston, South Carolina, Monday, engineering officials said they’ve found no risk of premature failure in the carbon-composite body for the roughly 1,100 Dreamliners flying commercially.
“There were zero findings of fatigue in the composite,” Steve Chisholm, a Boeing vice president of structural engineering.
The company faces mounting scrutiny of its manufacturing quality, and its safety culture will be the subject of congressional hearings in Washington this week. It’s grappling with a management shakeup stemming from a crisis of confidence after a fuselage panel blew off a different aircraft model, a 737 Max, during an early January flight.
The planemaker is also working to dispel claims levied by a company engineer last week that shortcuts taken during 787 assembly work could weaken the advanced aircraft’s structure prematurely. The company has denied those allegations, saying it’s found no sign of fatigue in maintenance checks of the plane’s composite structure performed on about two-thirds of the more than 900 Dreamliners assembled using a manufacturing technique flagged by the whistleblower.
The Boeing engineers said the issues prompting the latest planned inspection of the plane’s aluminum forward pressure bulkhead have nothing to do with the whistleblower’s claims. The company hasn’t identified any safety issues with respect to the management of gaps in the aircraft’s composite airframe, said Chisholm.
The recommended inspection is an example where Boeing has identified and is taking action to address a potential problem, he said. The planemaker is discussing the bulkhead issue with regulators, including when to perform the check, which should take about 10 hours per plane to complete, Chisholm said.
Whistleblower Response
The company invited journalists to the North Charleston facility to review steps it’s taken to address tiny structural flaws in the 787, whose fuselage is made by combining large sections of carbon composite barrels. The planemaker has tested the aircraft for fatigue over the equivalent of 165,000 takeoffs and landings, far in excess of the commercial service for a typical widebody jet.
“That’s actually the longest fatigue test of any commercial airplane that’s ever been run,” Chisholm said, noting the test took five years to complete.
The disclosures aim to rebut claims by Boeing quality engineer Sam Salehpour that the planemaker cut corners in assembling widebody jets in order to save time and get the planes to customers. Salehpour is slated to testify about his concerns Wednesday during a hearing held by the Senate’s Permanent Subcommittee on Investigations.
Boeing has said it is cooperating with the panel’s inquiry.
Salehpour, who worked on the 787 program from 2020 through early 2022, said the US manufacturer improperly measured and filled tiny structural imperfections in the joins between the mated composite barrels, applying excessive force to make the parts fit rather than going through the arduous process of shimming the gaps with tiny strips. The excess force may over time degrade the carbon-fiber structure, which has different properties than aluminum traditionally used on aircraft fuselages, Salehpour alleged.
Boeing officials said the forces used to join the components were thoroughly vetted and tested before being implemented on the production line, and were at a level of force negligible for hardened carbon composite barrels. “Whether it’s 150 pounds, or 50 pounds or 10 pounds. It’s a very small force for these products,” Chisholm said.
Even before the latest allegations became public, Boeing was under intense public scrutiny in the wake of a near-catastrophic accident involving an almost-new 737 Max 9 model early in January, which lost a fuselage section during flight. As a consequence, Boeing’s quality and production methods have come under the microscope from regulators, who have capped output of the 737 model to ensure the planemaker improves its processes.
Boeing’s board took its most decisive move yet in late March with a sweeping management shakeup in which Chief Executive Officer Dave Calhoun agreed to step down by the end of the year.
19 Steps
The 787, which is much larger than the 737 and is used for long-distance travel, had already faced years of scrutiny before Salehpour leveled his allegations.
Boeing halted Dreamliner deliveries for almost two years as it addressed the tiny imperfections about the width of a hair where carbon barrels are bolted together. Lawyers for Salehpour allege that even after regulators signed off on the fixes, the company continued to cut corners, a claim the company denies.
Any manufacturing changes to the 787 first face a detailed internal review and analysis, a 19-step process that involves a large group of participants and ultimately the Federal Aviation Administration, said Lisa Fahl, a Boeing vice president who oversees engineering teams across all airplane programs.
That was also true of the increase in so-called fit-up force on the 787, Chisholm said, adding the change was minor on a frame designed to bear thousands of pounds of force.
Salehpour also claimed to have witnessed problematic practices in the production of Boeing’s 777 aircraft that resulted in the misalignment of parts. Together, he believes these pose “potentially catastrophic safety risks,” according to correspondence between Salehpour’s attorneys and the FAA.
Boeing last week said it is “fully confident in the safety and durability of the 777 family.”
(Updates with engineer quote, details of inspections from second paragraph)
©2024 Bloomberg L.P.